人やモノに関与して新しい価値を創出することを支えるシステムが「Systems of Engagement」。具体的にはどのような取り組みがなされているのか。ここでは、航空業界を横断した部品管理システムの例を解説する。
富士通は、様々な形でSystems of Engagement (SoE)に属するシステムの開発に取り組んでいる。タクシー会社と組んだ交通状況の可視化、事業会社や農協との共創による農業のICT化などだ。ここでは、そんな例の1つとして航空業界を横断した部品管理システムを説明する。
企業を超えた部品管理を実現
航空機で何より重要なのが安全性(信頼性)である。それを担保するためにエンジンや制御装置など、様々な部品の適正な管理が必要であることは言うまでもない。当然、機材に取り付けられている部品の使用履歴や交換日時はデータとして厳格に管理されている。だが、そのための負担が大きいという問題があるのも事実だ。
具体的には、(1)航空機メーカーや航空会社、部品メーカー、整備会社などの間で、しかも国を跨がって部品を管理する仕組みが複雑、(2)必要な部品を速く入手できるようにするため高価な部品を重複して在庫するケースが多い、(3)部品交換などを間違いなくこなすために整備士の負担が高くなる、などである。複雑な部品管理に手を抜けない一方で、格安航空会社の急増、他の交通手段との競争などにより、コスト低減も急務になっている。
そこで米ボーイングや仏エアバスといった航空機メーカーのパートナーとして、富士通は「AIT(Automated IdentificationTechnologies:自動認識技術)」の一種であるRFID(ICタグ)を活用。主要な部品にRFIDを取り付け、使用履歴やメンテナンス情報を自動受け渡ししたり更新することで、上記の問題解決に取り組んでいる(図)。
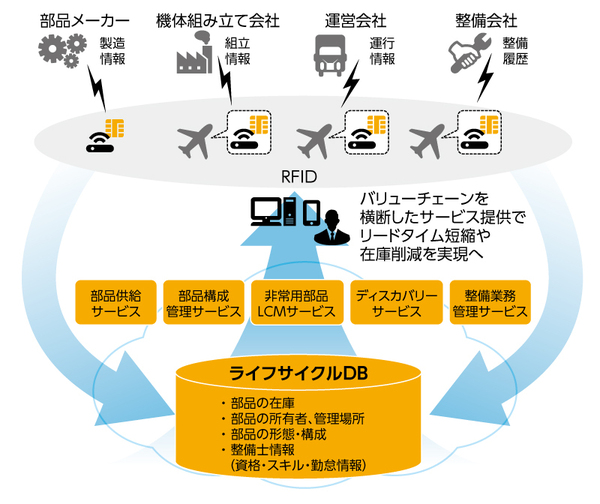
拡大画像表示
1機当たり3000の部品を可視化
具体的に見てみよう。航空機はざっと300万点の部品から構成される。このうちRFIDなどを取り付けるのは、主要な3000品目(今後拡大予定)である。機体の製造段階で、メーカー名や製造番号などが記された銘板の代わりに部品に取り付ける。
運航段階で整備や交換などがあれば、RFIDなどの情報は自動更新される。RFIDは最大64KBの容量があるので、部品の製造年月日やメンテナンス履歴に関するすべてのデータが蓄積・保持される仕組みだ。それらのデータはタグリーダで読み取り、機体ごとのDB(ライフサイクルDBと呼ばれる)にも保管される。
図Aでは、各部品のバリューチェーン(製造、組み立て、運営、保守)全体を俯瞰した部品の適用状況を把握できることを示している。それぞれのタイミングで発生する断片的な履歴情報がRFIDタグに蓄積されると共にライフサイクルDBで一元的に管理されるからだ。
つまりライフサイクルDBには、運航に供されている数万機の機体それぞれに関して、300万点の部品データと、トレーサビリティ情報がある3000点の部品データが蓄積されている。人に依存せず部品データの登録やメンテナンス履歴を保持できるため、実際の部品の所在とライフサイクルDBのデータが一致する。これにより、例えば部品の保管場所や在庫数をグローバルで管理し、タイムリーな交換部品の割当てや、重複調達の防止が大幅に容易になった。
部品管理システムはさらに進化へ
整備の効率化にも繋がる。航空機への搭載が義務づけられる非常用装備品の確認を例に取れば、RFIDタグに搭載場所の位置情報や装備品の有効期限を格納しておけば、タグリーダで読み取った情報を検査用プログラムで照合することにより、有効期限が切れた装備品を自動検出できる。銘板の情報を目視で確認するのに比べ、現場の点検・整備作業効率は大幅に向上し、確認/入力ミスもなくせる。
とはいえ、この種の取り組みは前例があるわけではない。要件や適用範囲を予め特定して開発を進めることは難しい。実証実験を繰り返しながら、そして効果を見極めながら、機種や機体などの適用範囲を順次拡大しているのが実情だ。例えば現在はパッシブなRFIDを使っているが、今後は通信機能付きのセンサーを利用する構想もある。
- 次世代ICT技術をどう取り込むか(2015/05/13)
- ICTが可能にする新たな価値創出(2015/05/13)
- 変化対応力の高い情報システムとは(2015/05/13)
- デジタルビジネス時代の情報システム像(2015/05/13)