製造業でAIの導入が急速に進んでいる。品質検査や故障予兆検知、サプライチェーンや製造プロセスの最適化など、ビジネスの根幹を担う領域にも適用が検討されている。しかし、日本の製造業の現場は海外と比較して導入が遅れているという。何が障壁になっていて、どのようにすれば、高い技術力を持つ日本のメーカーがAIを駆使して世界をリードする存在となれるのか。産業制御システム大手の米ロックウェルオートメーション(Rockwell Automation)アジア太平洋地域プレジデントのスコット・ウールドリッジ氏と日本法人代表取締役の矢田智巳氏に話を聞いた。
AIの導入は「1年遅れたら、5年遅れる」
近年、製造現場で、ITとOT(製造・制御システム・運用技術)の融合によるデジタル化が加速している。IoTセンサーとAIを用したリアルタイムモニタリングによる品質異常の迅速な検知や、従来、定期点検に依存していた設備管理でのマシンの稼働データ分析による故障の予兆検知/対処などは今や珍しくなくなっている。
産業制御システム大手の米ロックウェルオートメーション(Rockwell Automation)は、この領域に特化したベンダーとして製造現場のモダナイゼーションに力を注いでいる1社だ。2024年11月に米カリフォルニア州アナハイムで開催された同社の年次イベント「Automation Fair」では、マシンラーニング(機械学習)を活用した最新の品質検査システムを披露している(関連記事:AI・ロボティクス・SDA─米ロックウェルが示す製造業の将来)。
ロックウェルのシステムの特徴の1つに、従来のように人手で詳細な検査基準をプログラムする必要がない点がある。システムが多数の製品サンプルを観察・分析することで良品の特徴を自動的に学習し、その基準から外れる不良品を検知できる。「マシンラーニングやAIの適用で、今後は検査基準の細かなプログラミングやパラメータの調整作業までもが不要になる」というのがロックウェルの見立てである。
製造業にかぎった話ではないが、AIの導入は「1年遅れたら、5年遅れる」と言われている。生成AIをはじめとする今日のAIは実際の業務データを基に学習・改善を続けることで精度が向上していく。そのため、導入の遅れは単なる時間的な遅れではなく、データ蓄積・学習による進化の機会をロストすることをも意味する。先行企業とのギャップは、時間の経過とともに加速度的に広がっていくのである。
残念ながら、日本の製造業におけるAIの活用はすでに海外に後れを取っていると言われる。なぜだろうか。この点についてロックウェルオートメーション ジャパン代表取締役の矢田智巳氏(写真1)は、「技術的な課題よりも、組織体制や人材不足といった企業全体が抱える課題だ」とし、以下のように説明する。
「経営層はAI活用の必要性を理解しているものの、実際の導入・推進体制の不足が大きいと考える。よく言われていることだが、日本ではCIOが不在の企業も多く、社内で最新のテクノロジーを理解し、経営課題の解決に結びつけられる体制が整っていない」
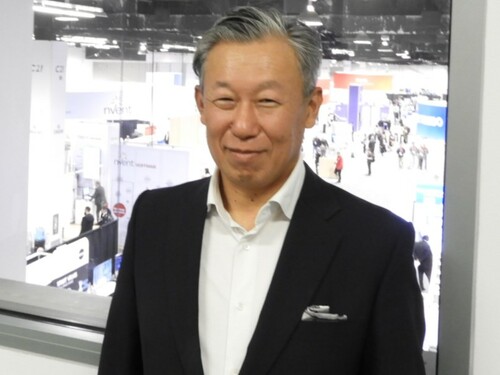
●Next:リーンやシックスシグマが根づいているなら、AIの活用はうまくいくはず
会員登録(無料)が必要です
- 1
- 2
- 3
- 次へ >