エイムネクストは2011年3月24日、工場設備と基幹システムの連携を検証する施設「エイムネクスト スマート・ファクトリー デモセンター」を公開した。工場のラインを再現し、日本インフォア・グローバル・ソリューションズのERP「Infor ERP LN」を使って設備機器などの稼働状況をモニタリングできる環境が整う。工場における情報のリアルタイム収集で、品質管理の向上や管理コスト削減など提案する場と位置付ける。
エイムネクストは「スマート・ファクトリー」と呼ぶ工場マネジメントシステムのコンセプトを提唱する。これは、工場内の設備や管理機器と基幹システムをネットワークで結び、一元化した情報を共有できるようにするもの。従来は設備機器ごとに異なるインタフェースや通信プロトコルを用いていたため難しかったが、「ネットワークのオープン化が進んだほか、機器を監視するセンサー類も安価に購入できることから十分可能である」(代表取締役社長 清 威人氏)という。
具体的には、MES(製造工程の状況管理や作業を指示するシステム)やPLC(機器の制御装置)、設備/検査機器、各種センサーをネットワークで接続する。独自プロトコルを用いる設備機器については、プロトコルを変換する「OPC(OLE for Process Control)サーバー」を設置して対処。既存設備をネットワーク環境に取り入れることも可能だ。こうして集めたデータを、分析しやすい管理指標に変換して見える化する。
例えば、加熱処理する部品の温度を監視し、事前にしきい値を設定しておくことで、上限温度を超えた部品を不良品として洗い出せる。温度がしきい値に達しそうな段階でアラートを出し、不良品の発生を防ぐことも可能だ。部品ごとにラインを通過した際の情報を保持しているため、製品に不具合が見つかった場合、部品別にどの過程に原因があったのかを遡って調べられる。
「メーカーの品質保証に対する要求は厳しく、工場側は設備や工程を変更する度にメーカーに報告しなければならない。そのため、報告用の書類を作成する間接業務の負荷増加が問題となっている。スマート・ファクトリーを取り入れることで、人手に頼らず品質に関するデータを容易に収集できる。書類作成に要する時間短縮も見込める」(清氏)。
デモセンターは2011年3月1日より稼働しており、すでに50社程度の企業が視察に訪れたという。導入プロジェクトも国内で2社、海外で1社が進行中だ。
同社は日本インフォアと共同でコンサルティングにも力を入れる。「スマート・ファクトリーを実現するためには、技術的な施策だけではなく、人や組織、業務手順の見直しも不可欠である。特に情報システム部門と設備部門が連携し、業務改革を推進する組織の構築が必要である」(清氏)と指摘する。
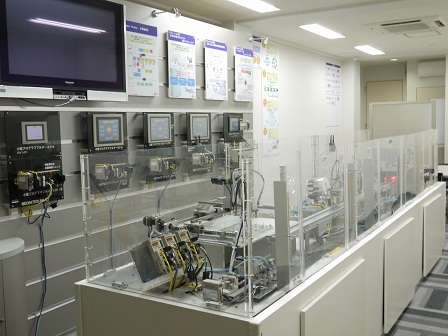