印刷用インキなどを製造する化学メーカーのDIC(本社:東京都中央区)は、製造現場の設備や作業者のデータを収集・蓄積・分析するシステムを同社館林工場に導入した。マクニカの「DSF Cyclone」を採用し、従来、設備からのアラート発生時、現場担当者が毎回現地に赴く必要があり、生産現場の状況把握が難しかった問題を解決した。マクニカが2024年9月24日に発表した。
DICは、印刷インキや有機顔料などを製造する化学メーカーである。樹脂着色剤事業のマザープラントであるDIC館林工場(群馬県館林市)では、2017年ごろから生産部門を中心にデジタル化を進め、スマートファクトリーを推進してきた。
しかし従来のシステムには課題があった。設備からアラートが発生した際は、現場担当者が毎回管理室や現地に赴く必要があり、無駄な移動や対応の遅れが生じていた。収集したデータを有効に活用する環境も整っていなかったという。
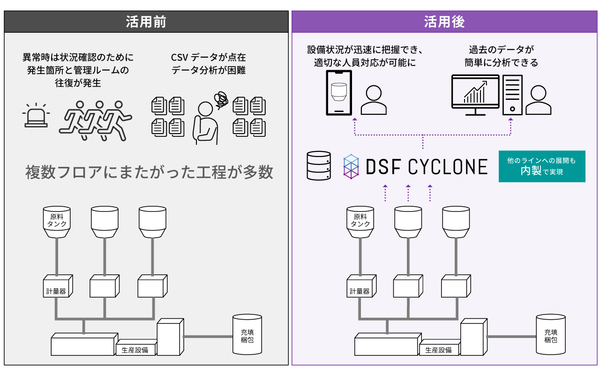
拡大画像表示
そこで、館林工場に設備を遠隔監視し、データ分析を行うマクニカの「DSF Cyclone」を導入した。データの収集・正規化・分析を1つのパッケージにしたシステムで、製造現場と生産管理を実績データでつなぐことでデータドリブンな工場運営を支援する(図1)。
館林工場は4階建てで、20以上のラインが稼働している。遠隔監視の対象となるラインを段階的に増やしていくにあたって、外部ベンダーにつど依頼するのではなく、内製で対処できることを重視した。「項目の追加や画面の変更にも内製で対処したかった。DSF Cycloneは、現場でデータを簡単に活用する機能を備えており、当社の内製化ニーズに合致した」(DIC)。
同工場の2つのラインにDSF Cycloneを導入している。設備の稼働状況を確認するための専用画面も作成し、スマートフォンなどから異常の発生などを迅速に把握できる。例えば、原料タンクの中身が減れば補充する必要があるが、スマートフォンで原料タンクの状況を可視化したことで、どこにいても補充すべきタイミングが適切に判断できるようになった。
DICは、DSF Cycloneによって現場が可視化できるようになったことで、機械がフル稼働した場合に削減できる時間を1日あたり260分と試算している。
今後は、DSF Cycloneを活用してデジタル人材を社内で育成し、現場の要件変更に内製で迅速に対応可能な体制を整える。また、収集したデータの利活用をさらに進め、精度の高い生産計画を立て、トラブルに対応する。また、システムを改善し、新機能やデータポイントの追加によって、より多くの情報をリアルタイムに把握できるようにするとしている。