印刷用インキなどを製造する化学メーカーのDIC(ディーアイシー、本社:東京都中央区)は2024年12月5日、合成樹脂製造プラントの運転をデジタルツインで自動化するシステムを、同社国内工場で2025年1月に稼働開始すると発表した。2021年から日立製作所と共同で実工場での実証を行い、製造工程における反応状態の予測と最適運転条件の探索技術を確立し、実用化に至った。今後、DICの国内3拠点、海外1拠点に展開する予定である。
印刷用インキなどで知られる化学メーカーのDICと日立製作所は、2021年3月から合成樹脂製造プラントの運転自動化を図るデジタルツイン技術の実用化に向けた協創に取り組んでいる。
第1フェーズでは、DICの国内3工場で製造する樹脂製品を対象に反応予測モデルを構築・検証。これまで熟練者の経験則で感覚的に認識していた反応影響因子を定量的に把握できるようになった。これを受けて業務の属人化からの脱却を進めている(図1)。
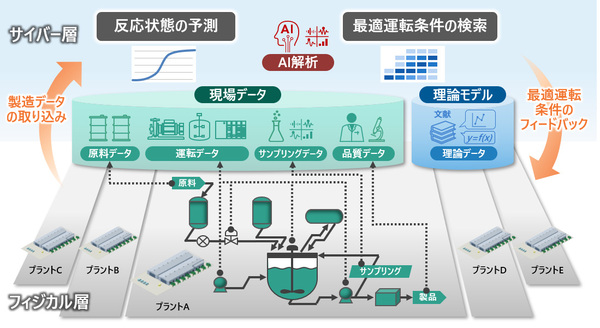
拡大画像表示
「一般的な合成樹脂のバッチ生産においては、製品品質確保のため、反応工程の途中で人によるサンプリングや分析、反応進捗判断の作業を繰り返しながら、調整原料を投入している。反応工程中だけでなく、反応前工程の温度、圧力などの動向が製品品質に影響を与えるため、全工程にわたる運転状況の把握と考慮が不可欠である」(DIC)。同社によると、作業は煩雑かつ属人的になる傾向があり、製品の品質検査合格率がばらつく課題もあったという。
DICが開発したシステムでは、AIなどを用いた反応予測モデルと共にサイバー空間上にプラントの運転状況を再現したデジタルツインを構築。プロセスインフォマティクス(PI)を活用して目標とする品質値に向けた調整タイミングや投入量を決めるための最適な運転条件を導き出し、これらをフィジカル空間(現場)にフィードバックする。これにより、サンプリング確認回数の低減、品質の安定化、作業員の作業効率向上、新製品導入時の立ち上げ期間短縮などを目指す。
目標とする品質値(粘度など)を得るための運転条件(調整タイミングや投入量など)を自動で算出し、「ヒートマップ」(画面1)として作業員に明示。バッチ生産に適切な運転条件を選択できるようになる。約20回のバッチ生産運転データだけで、化学品製造に活用できるモデルの作成が可能だとしている。
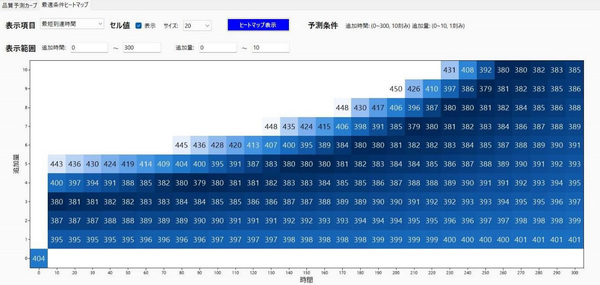
拡大画像表示
ヒートマップは、製造時の追加原料量(縦軸)と追加タイミング(横軸)の組み合わせで、製品品質が所定の値に到達するための最短運転時間の予測結果を可視化する。作業員は、現状の予測結果から高い効果を見込める運転操作を選択できる。色の濃淡は運転時間の差を表し、濃いほど短い時間となる。
システム画面に表示する粘度などの「品質予測カーブ」により、反応中の手動サンプリング分析操作を行うことなく、現在の製品品質、将来の品質の推移、反応工程が終わるタイミングを確認可能である。過去の運転実績と比較する機能も備えており、作業員が納得感をもって運転条件を確認可能だとしている。
今後、DICの国内3拠点、海外1拠点に展開する予定である。バッチ生産における巡回点検や原料の搬出入作業のロボティクス化、各システム間のデータ入力作業や生産計画立案の自動化など、より高度な自動製造システムの実現を目指す。さらに、製造実行領域だけでなく、サプライチェーンを含めた全体の最適化・効率化に向けた取り組みを検討する。