[インタビュー]
「IoTが日本の“ものづくり”を進化させる」印TCSのエンジニアリング担当トップ
2016年7月28日(木)志度 昌宏(DIGITAL X編集長)
経営のデジタル変革において、製造業者の多くが注目するのがIoT(Internet of Things:モノのインターネット)だろう。“ものづくり”の現場である工場の改革と、モノを販売した後の顧客接点の拡大という2大改革を可能にするからだ。その製造業におけるIoTへの取り組みに向けたサービス体制を急拡大しているインテグレーターの1社にインドのTata Consultancy Services(TCS)がある。米GEと戦略提携を結び、IoT基盤「Predix」の利用も支援する。TCSはIoTをどうとらえているのか。来日した印本社副社長で製造業向けサービスをグローバルに統括するRegu Ayyaswamy(レグー・アヤスワミー)氏に聞いた。
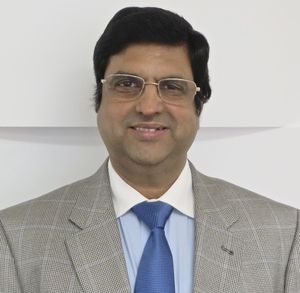
──IoT(Internet of Things:モノのインターネット)への関心が高まっている。グローバルにサービスを展開する企業として、世界の動きをどのように見ているか。
IoTというキーワードが注目され始めたのは2〜3年ほど前からで、概念が先行してきた。多くの企業がPoC(Proof of Concept:実証実験)の段階にあるが、ここにきて本番稼働に乗り出す企業の姿も見られるようになってきた。
私は製造業担当として日本にも10年以上前から訪れており、産業機器や自動車、家電といった各種の顧客と対話してきた。その経験からいえば、日本企業にとってIoTはビジネスモデル変革のための大きなチャンスになると確信している。IoTによって設計から製造、サービスまで、製品のライフサイクル全般をつなげられれば、生産性の向上を含め、バリューチェーンそのものを一新できるからだ。
日本は、最高の製品を作るという“ものづくり”に取り組み、そこでは世界的な競争力を持つ良い結果を生みだしてきた。それを土台にすれば、前工程の設計や後工程のサービスにまで各社のバリューチェーンを早期に拡張できるだろう。当社ではそうした仕組みを「Connected Enterprise」と呼んでいる。設計、製造、サービスをシームレスかつリアルタイムにつなぐ。システムでいえば、PLM(Product Lifecycle Management)とERP(Enterprise Resource Management)
とMES(Manufacturing Execution System)がリアルタイムにつながった状態である。
──先行企業は、どんな仕組みを動かそうとしているのか。
日本の自動車メーカーの例を紹介しよう。自動車では数々の診断データが取得されているが、その自動車メーカーでは、世界にある1万5000カ所のディーラーを経由して、すべての診断データをクラウド上に収集するとともに、そのデータを分析・参照するためのダッシュボード機能を構築しようとしている。
クラウド上に集めたデータは、設計上の改善点を見いだすために利用するほか、製造や保守サービスなどグループ内の複数部門が利用する計画だ。これにより、自動車の信頼性や顧客満足度を高めると同時に、故障などに対する保証コストの削減を狙っている。
TCSとしてもIoT関連プロジェクトに取り組んでいる。オフィスビルを対象にしたエネルギーマネジメントの仕組みで、2014年11月に開始し2016年1月に本番稼働させた。当社はインド国内だけで100以上の拠点を持っているが、それらすべてを対象に空調や発電機など1万を超える機器の稼働状況と、ビル内にいる人の数や温度などのデータを5分間隔でクラウドに集計、運用の最適化を図ることで電力消費量を10%削減できた。
従来はビルごとに異なるビル管理システムを導入し利用してきた。メーカーも様々で、それぞれのシステムが持つ機能の範囲内でしか運用できなかった。今回、IoTの仕組みを使ってデータを統合したことで、ビル間や機器間でデータを比較することで最適な運用になっているかどうかが分かるほか、各フロアで働いている人の数に合わせて空調運転を変えるなど、より多くの要素を加味しながら、より最適な判断を下せるようになっている。
他にも北米のトラックメーカーが稼働させたエンジンの診断や積載物の追跡のための仕組みや、医療機器メーカーの取り組みといった事例がある。
──先行企業と一般的な企業の間に違いはあるか。
先行企業は、IoTを変革のための「ビジネスエネーブラー(テコ)」と考え、全社横断による全勢力を注いでいる。PoCあるいは、それ以前の企業はまだ探りを入れている段階だ。IoTに取り組むための目標が定まっていないとも言える。
会員登録(無料)が必要です
- 1
- 2
- 次へ >