熾烈な競争にさらされる日本の製造業にとって、IoTやAIといったデジタル技術を駆使した生産の自動化やそれによる抜本的な生産性向上は、喫緊の課題だ。言わば”スマート工場”の実現だが、それは「言うは易し行うは難し」の典型でもある。ここに紹介するカシオ計算機は、システムの多くを内製して工場のスマート化を実現している。同社執行役員 生産本部長の矢澤篤志氏と、生産本部 生産技術部 技術戦略室 アドバイザリー・エンジニアの鈴木隆司氏に、その取り組みを聞いた。
スマート工場を実現するとなると、先進的なツールやソリューションを導入すると大きな投資が必要になるし、自前でやろうとするとノウハウやスキルを有する人材が不在といった問題に直面する。PoC(概念実証)レベルならともかく、実用化は今なおハードルが高いと言ってもいい。
そんな中、カシオ計算機から「うちのIoTやAIの活用事例を取材しませんか」という話があった。カシオは「G-SHOCK」に代表されるウォッチ、海外の文教市場で好調な電卓、電子ピアノなどの電子楽器といった個人向けのほか、レジスターなど企業向け製品も扱うメーカー。そのすべてではないが、まずは製造コストの低減や生産性向上が至上命題である低価格帯のウォッチや電子楽器の製造設備に対してIoTやAIを活用、大幅な自動化と効率化を達成したという。
嫌も応もない。実際にどんなふうに活用しているのかを、スマート化の指揮を執った同社執行役員で生産本部長を務める矢澤篤志氏と、現場で実務を担った生産本部 生産技術部 技術戦略室 アドバイザリー・エンジニアの鈴木隆司氏に聞いた。詳細は後述するが、国内に唯一ある生産拠点の山形工場をマザー工場とし、そこでIoTやAIを内製するのが基本。その上で中国やタイなど海外にある4工場へ展開を進めている。以下、Q&A形式でお届けしよう。
生産技術の蓄積と自動化推進がスマート工場のきっかけ
──IoTやAIを活用してスマート工場に取り組んだ背景を教えていただけますか。
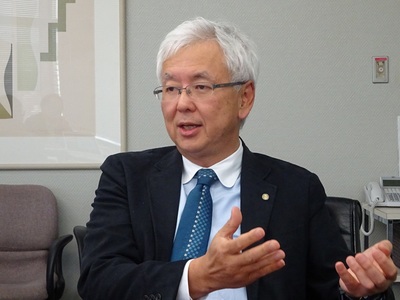
矢澤氏 その話をする前に、当社における生産の歴史を説明させてください。その方が分かりやすいので。まず1980年代までは国内生産が中心でしたが、1990年代に入り一気に海外生産が進み、2000年頃には国内に4、海外に13の生産拠点がありました。しかし2001年に初の赤字決算になり、生産拠点の統廃合を進めて国内は1拠点、海外も4拠点にまで減らしました(図1)。
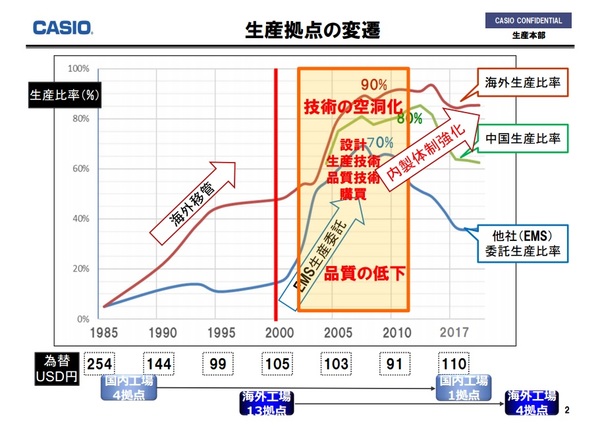
拡大画像表示
──20年前の話ですけど、凄まじいですね。
矢澤氏 ええ。当然、この工場数では生産を賄い切れませんから、いわゆるEMS(電子機器の生産委託事業者)への委託が急増しました。ウォッチは内製を維持していましたが、それ以外のほとんどの品目はEMSに依存していて、2007年のピーク時には7割にまでなります。でもそれ以降、EMSの割合は減っていきました。
大きな理由は中国や台湾のEMS事業者の変化でした。我々が委託するのは多品種少量の案件だったのですが、EMS事業者は効率のいい携帯電話やスマートフォンなど量産品にシフトしていたんです。この時期、当社においても生産技術が蓄積されない問題が浮上していました。そこでEMSへの委託比率を下げ、内製を強化する方向に転換したのです。
──とはいえ、それはそれで大変ですよね?
矢澤氏 もちろん急には転換できませんけど、2010年代に入ると海外の人件費が高騰し、労働集約型の生産が限界に近づく状況もありましたからね。結果として品質や生産性をしっかり確保し、海外拠点に対して技術支援できる国内拠点が必要という考えに至りました。最終的には国内唯一の生産拠点だった山形工場(写真2)を「マザー工場」にするという方針を決めました。
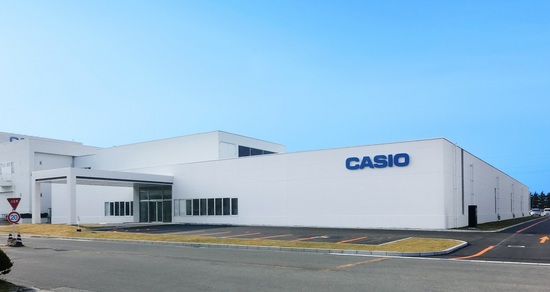
──山形工場には、そのポテンシャルがあった?
矢澤氏 ええ。山形工場は現在ではウォッチの製造が主力ですが、以前は携帯電話を製造していました。そのために2000年頃には3次元CADから金型を製造したり、生産設備の稼働状況をモニタリングする、今でいうIoTの取り組みも行っていました。生産設備も担ってきた拠点なんです。
国内唯一の製造拠点ということもあって中国の3拠点、タイの1拠点、一部EMSの量産前の工程も含めて技術的にサポートするマザー工場として位置付けました。山形工場で日本標準の高い製造品質を達成し、ウォッチだけでなくすべての商品に対して技術展開を図ることにしました。
使っているソフトは、まず富士通の3次元CADである「iCAD」です。設計から組立シミュレーションや工程の設計などを行います。以前、当社でも同様なソフトを作っていたのですが、他の工場に横展開するために汎用のパッケージ製品を用いました。
それからPTCのIoTプラットフォームである「ThingWorx」を採用しています。山形、中国、タイの各工場に展開して設備の稼働状況を監視するのが目的で、稼働状況は東京都羽村市の生産本部に集約しています(図2)。生産ラインを立ち上げる際には色々な問題が起こるので、その問題やラインの組み換え、タクトタイム(工程作業時間)の調整も含めて状況を見ながら山形から改善を指示し、安定化するまでサポートしています。
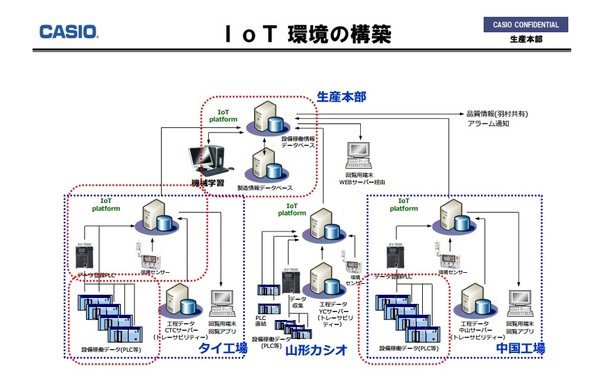
拡大画像表示
●Next:山形工場のスマート化、まず始めたのは?
会員登録(無料)が必要です
- 1
- 2
- 3
- 次へ >
- 「こんな旅がしたい!」をチャットの対話で提案、Booking.comが挑むAI駆動の旅行計画(2025/08/05)
- 脆弱性対処を10日から3日に─JERAが実践するマルチクラウド環境のセキュリティ強化(2025/07/31)
- コラボレーション・自動化・AI─全社ファイル管理基盤を核にしたオンワードグループのDX実践(2025/06/30)
- 『モンスターハンターワイルズ』の開発で、カプコンのITチームが重視したこと(2025/06/11)
- 生成AIとロボットの融合で新たな価値創造に挑む─デンソーが描く近未来(2025/04/22)
スマート工場 / Raspberry Pi / ThingWorx / カシオ計算機 / デジタルトランスフォーメーション / PyTorch / Chainer / 3DCAD