東洋製罐(東京都品川区)は、製品マスター管理システムを、ローコード開発とアジャイル開発で構築した。スクラッチ開発の試算と比べて、工数と工期を3分の1に削減した。ローコード開発ツールの機能により、ドキュメントの量も従来比で約9割削減した。SIベンダーのTISとローコード開発ツールベンダーのOutSystemsジャパンが2022年4月13日に発表した。
東洋製罐は、製品マスター管理システムを、ローコード開発とアジャイル開発で構築した。スクラッチ開発の試算と比べて、工数と工期を3分の1に削減した(図1)。スクラッチ開発の試算では、再構築に200人月の工数と2年6カ月の期間がかかる。これを75人月、9カ月で再構築した。ドキュメントの量も、ローコード開発ツールの機能により、従来比で約9割削減した。
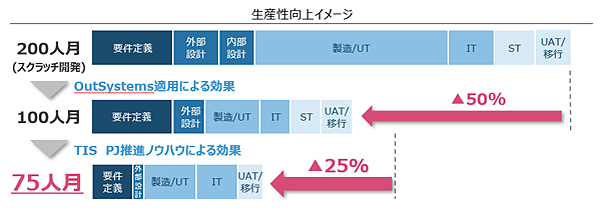
東洋製罐グループホールディングス(東洋製罐GHD)の方針は、コア業務についてはグループで共有するERP(統合基幹情報システム)を構築し、グループ各社の固有業務機能を共通アーキテクチャに基いたシステム開発で補完するというもの。これにより、情報の一元化と、事業環境変化への柔軟な対応を両立させる。この取り組みの1つとして今回、米/ポルトガルOutSystems(日本法人:OutSystemsジャパン)のローコード開発ツール「OutSystems」を用いて製品マスター管理システムを再構築した(関連記事:TIS、ローコード開発基盤「OutSystems」の導入支援サービス、ノウハウをテンプレート化)。
従来の製品マスター管理システムは、業務部門の担当者自身がデータベース開発ツール「Microsoft Access」を用いて約10年前に開発したもの。150以上の機能を備えて、約50種類の製品と約30万件のデータを管理している。現状の業務にそぐわないことが多かったため、今回再構築したという。
再構築にかかる工数と時間の削減を目的に、ローコード開発ツールを活用したアジャイル方式を採用した。スクラッチ開発に比べて2~3倍の開発生産性向上が期待できるからである。実機で仕様を確認できる点もローコード開発のメリットだった。東洋製罐では仕様を理解している業務担当者が1人しかおらず、ドキュメントのレビューの負荷が課題だったが、動くシステムをその場で作成して仕様を確認するやり方がとれた。
OutSystemsの機能により、ドキュメントの量も従来比で約9割削減できた。同ツールのモデルに入力した設定が、そのまま設計書などドキュメントとして使えるため、ドキュメントの作成作業や管理作業が不要になった。また、システム改変の履歴を自動で記録することから、ドキュメントの整合性を容易に維持できるようになった。