多くの製造業がスマートファクトリー/DXを目指した取り組みを加速させているが、実際にはPoCで立ち止まっているケースも珍しくない。ほぼすべての施策に業務プロセスの変更や部門間連携が伴うため難易度が高すぎて、「わかっているけど思うように進まない」という閉塞状況に陥っているのである。ここで改めて認識する必要があるのは、デジタル化はあくまでも手段であることだ。データを使って経営をどのように変革していくのかという観点から、製造DXへのグランドデザインを描くことが重要である。
マクニカが考えるスマートファクトリー/DX成功の3要素
不確実性の高まる市場環境や事業環境に適応し、持続的な成長を遂げていくため、あらゆる企業にデジタルトランスフォーメーション(DX)が求められている。製造業も例外ではなく、多くの企業が生産現場からの設備データやセンサーデータの取得、さらにそれらのデータのAI分析などに乗り出している。
こうした取り組みの先に見据えているのが「スマートファクトリー」であり、経営と製造がリアルタイムに連動した変化に対応するための、データドリブンなリソース再配分の意思決定や、在庫と納期、品質とコストなど利益相反関係にある要素の最適化を目指している。
一見このDXジャーニーに間違いはないように見える。しかし、実際には、生産現場から取得したデータからボトムアップでDXを実現しようとするアプローチは成功が難しい。現に、上述した取り組みの多くがPoC(Proof of Concept:概念実証)から先のステップに進むことができず、頓挫してしまっている。スマートファクトリーやDXは、まさに「言うは易く行うは難し」である。
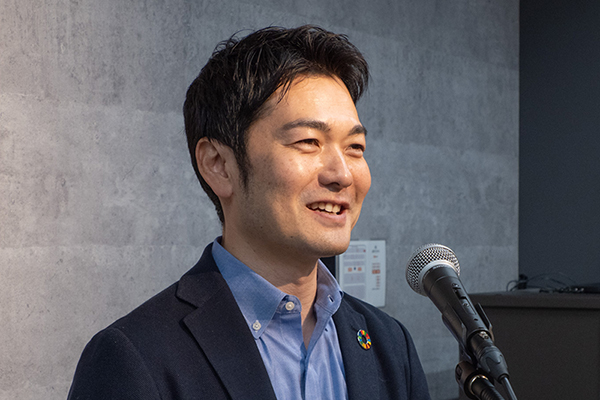
マクニカの阿部幸太氏は、スマートファクトリー成功のために必要な要素として、次の3つを示している。
1つめに「人」。スマートファクトリー/DXはあくまでも手段であり、一回やって終わりではなく継続的な取り組みが重要だ。そのコアの部分となるプランニングは内製が基本となり、重い負荷と高い期待値を背負うDXリーダー人材をサポートしなければならない。
2つめに「技術」。製造DXの特徴はITとOT、サイバーとフィジカルの融合にあり、単一の技術で目的が達成することはほぼありえない。複数技術の組み合わせによって実行可能な手段へと昇華させなければならないのだ。
そして3つめに「インフラ」。人の負荷を減らし改善サイクルを回すためには、必要なデータを自動的に取得して使える状態とするインフラが必須となる。とはいえ一気に莫大な投資を行うことはできず、最小限の投資で段階的に構築していく必要がある。
「結局のところ、会社として本当にやるべきことは何かが議論されないままスマートファクトリー/DX に突き進んでも上手くいきません。とにかくデジタル化さえ進めれば何とかなるというのは幻想にすぎません」(阿部氏)。
ダイナミック・ケイパビリティを高める経営観点のデータマネジメント
「経営としてデータをどう使っていくのか、あるいはデータを使って経営をどのように変革していくのか、あらためてじっくり考えてみるべきです」と説く阿部氏が、経営観点でのデータ活用のグランドデザインを描く上で、ベースとなる考え方として示すのが「ダイナミック・ケイパビリティ」である。
ダイナミック・ケイパビリティとは、もともとカリフォルニア大学バークレー校のデイヴィッド・J・ティース氏によって提唱されたもので、経済産業省・厚生労働省・文部科学省が共同で発表した「ものづくり白書2020」の中で取り上げられ、「日本の製造業の課題を考えるにあたって注目すべき戦略経営論」と位置付けられている。
端的に言えば「環境や状況が激しく変化する中で、企業がその変化に対応して自己を変革する能力」であり、脅威や危機を感知する「感知(センシング)」、機会を捉えて競争力を獲得する「捕捉(シージング)」、さらにその競争力を持続的なものとするため組織全体を刷新する「変容(トランスフォーミング)」の大きく3つの能力に分類される。
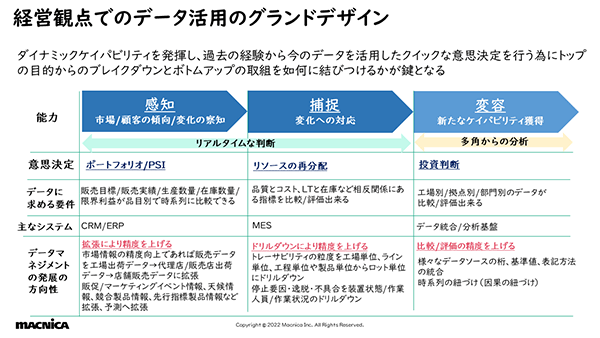
拡大画像表示
阿部氏はこの3つの能力を、データマネジメントの観点に基づいて次のようにブレイクダウンしていく。
1. 感知
まず「感知」だ。データマネジメントにおける1丁目1番地は市場や顧客であり、その変化点をいかに察知できるかがポイントとなる。たとえば新製品や企画品の投入、既存品の継続打ち切り、減産/増産などを判断する際に、事業責任者が市場の情報/変化点を素早く正確に知る必要がある。
ここでのデータマネジメントを発展させる方向性は取得データの拡張である。製造業であれば出荷データは精緻に追うことが出来るが、その先の販売会社や代理店、小売り店の在庫、エンドユーザーへの販売状況、イベントや気象、自社製品と相関性が高い(先行指標としてベンチマーク出来る製品/市場)の動向など様々なデータを連携させることで、正しい自社製品の市場評価が獲得でき、予測への発展が期待出来る。
2. 補足
変化を察知したならば、次はその変化に対応する必要がある。すなわちこれが「捕捉」である。「製造拠点や人員の差配などヒト・モノ・カネをどう動かすのか、勘と度胸ではなくデータに基づいて初動までの時間をいかに短縮できるかに、この能力は帰結していきます」(阿部氏)。
「補足」では、データマネジメントを発展させるアプローチが、先述した「感知」とは違うことを認識することが大事だ。この領域では、ドリルダウン(データの掘り下げ)により、変化に対応するための意思決定の精度を向上させていくのが効果の高いアプローチとなる。
わかりやすいところは、トレーサビリティの粒度である。トラブルがあった際どこまでの製品を隔離/調査しなければいけないかなど、判断の速度とトラブルシュートに掛かるコストにダイレクトに効いてくる。増産/減産の判断も、「工場、工程毎に何の製品をどの程度作ることができるのか」「完成品だけではなく、仕掛、原材料がどこにどれだけあるのか」などを、判断したいタイミングでドリルダウン出来ることが大事になる。
冒頭に話をした設備データやセンサーデータを使ってより判断の精度を上げていくためには、経営で行いたい判断からのドリルダウンとつながることが大事になる。製造現場のデータ活用は構造化されていないうえに、粒度の細かいデータを取り扱わなければいけないため、ハードルが高い、一見、現場の改善という観点でデータを活用してスモールで始められると思いがちではあるが、その取り組みを本当に活用するためには、そのデータを取る目的が明確になっている必要がある。
3. 変容
この先に見えてくるのが「変容」である。ここでは、リアルタイムというポイントは薄れるかわりに正しい判断が求められるため、比較検討が可能な形でデータを溜める必要がある。システムの投資より、データをどう管理していくかというポリシーとルールとデータの運用(誰の責任でどうデータが更新されていくか)という観点がより重要になってくる。
国や地域ごとの設備生産能力や生産拠点/ライン別の生産可能品目を可視化し、工場の増設/閉鎖、他社工場の買収、新たな設備投資など、重要な経営判断をシミュレーションやデータドリブンによって行うことが可能となる。
DX推進の“シェルパ役”となって伴走する
日本の製造業は、ここまで述べてきたようなダイナミック・ケイパビリティをいかにして獲得することができるだろうか。DXを本気で実現しようとすればするほど、ツールやシステムの話ではなく、人財と業務プロセスそのものの分析と変革を伴走する必要があるとマクニカでは考えている。
日本の製造業がDXにより部分最適から全体最適にシフトすることで変化に対する機動力を獲得するために、まず初めの一歩として必要なのは、部門を超えたコミュニケーションを円滑に行えるようにすることだ。ここでは、コミュニケーションを円滑にするための取り組みを紹介したい。
- 業務プロセスの可視化/標準化
- シミュレーション
- 仮想データ統合基盤
1. 業務プロセスの可視化/標準化
業務プロセスの可視化/標準化とは現状の正しい把握のことだ。レイヤー間/部門間のコミュニケーションのために必ず出発点を合意する必要があり、DXチームの多くが必要性を感じているものの、さまざまな障壁があり着手できていないケースが多い。
マクニカは、部門間/レイヤー間で共通する客観的かつ定量的な現状分析を行い、業務プロセスの可視化をクイックにローコストで実現できるよう支援する。
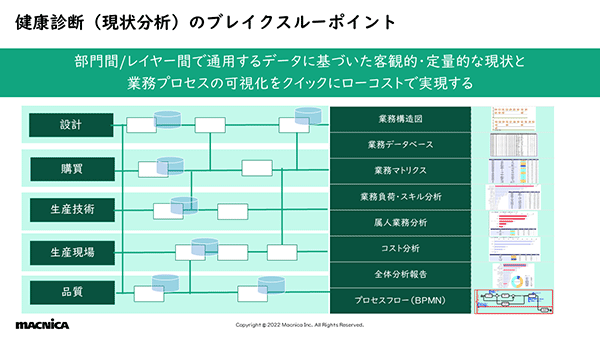
拡大画像表示
2. シミュレーション
体験の共有に勝る施策はない。そのため、工場などの製造現場をシミュレーションして可視化し、検証・予測して共有することは有効な施策となる。その際には、細部を作り込みすぎず、全体の傾向を掴むことが重要だ。
マクニカが提供する「デジタル工場導入支援サービス」では、7割~8割の精度で工程・工場を再現し、大まかな傾向を把握するというステップを短期間で準備し、調査負担少なく低コストで実現する。それをもとに、さまざまなシナリオを遺伝的アルゴリズムで最適化し、最適なシナリオを見つけ出していくことが可能だ。
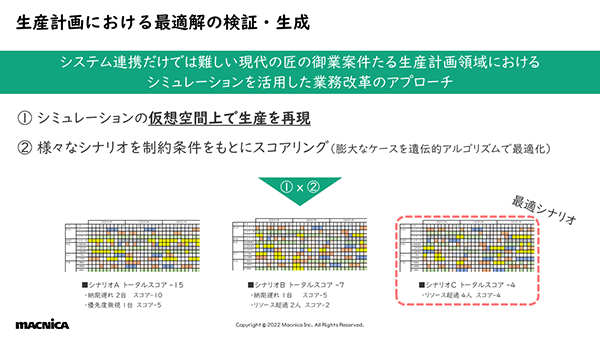
拡大画像表示
3. 仮想データ統合基盤
製造業では歴史的にそれぞれの部署で磨きこまれたさまざまなシステムが存在する。データドリブンな判断を行うためには、複数のシステムのデータを統合する必要があるが、そのハードルは極めて高い。また、インフラ側を整備してから出てきたデータで様々な判断を行い、データドリブンな経営にしていくというのも、一見、理に適っているように聞こえるが、非常に難しい。何のためにどのデータをどの粒度で見たいかを先に決めてから、必要に応じてインフラを整備していく必要がある。その「何のデータをどう見たいか」をクリアにするアプローチが「仮想データ統合基盤」である
仮想データ統合基盤は、複数システムの情報を検索性高く、クイックに突合出来る分析基盤を刺している。まずはデータ活用の効果の実感、体験をすることそのものがデータドリブンのマネジメントの始まりになる。
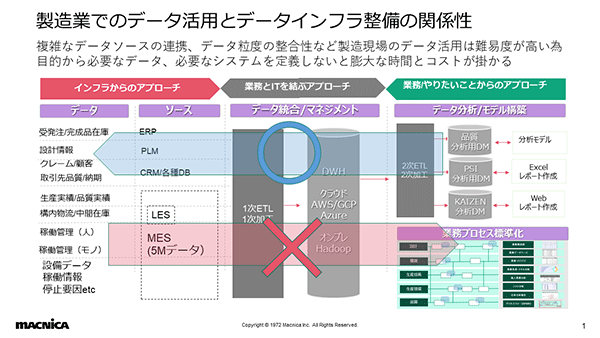
拡大画像表示
阿部氏は最後に、「DXのプランを立てるところは企業の内部で知恵を絞らなければなりません。ですが、様々な経験知見を取り込み、組み合わせるという観点で外部の力は借りた方がいい。丸投げはしないけど、無理もしない。そのためには、内部のコア人材と外部のプロ人材を混成した“ONE TEAM”で走り出すことが大切です。マクニカは、製造業におけるDX推進の「シェルパ(案内人)」となり、多様なソリューションをトータルで取り揃えて、お客様の取り組みに最初からゴールまで伴走させていただきます」と力強くアピールした。
●お問い合わせ先

株式会社マクニカ
URL:https://go.macnica.co.jp/contact.html
- カギは一元管理とモビリティにあり! マルチクラウド環境のデータ保護の最善策とは(2022/05/18)
- 企業に真のデジタル変革をもたらすロードマップの描き方とは?(2022/05/17)
- マスターデータマネジメント(MDM)導入を成功に導く“顧客主導型”アプローチ(2022/05/16)
- DX時代のストレージに求められる要件を“攻め”と“守り”の両面から満たすピュア・ストレージ(2022/05/13)
- ITよがりのデータ品質の考え方から脱却した「成功するデータ統合基盤づくり」のツボ(2022/05/12)