部分最適をいくら極めても、サイロ化したシステムをバッチ処理で連携させていては、いずれ製造業は立ち行かなくなる─。そんな思いから富士通フロンテックは、モノと情報の流れをリアルタイムで管理するサプライチェーンマネジメントシステムを開発。社内組織にとどまらず、サプライヤー200社にまで利用対象を広げたシステムの全容をプロジェクトの指揮官に聞いた。聞き手は本誌副編集長・川上 潤司 Photo:陶山 勉
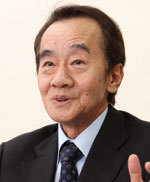
- 南里恒裕氏
- 富士通フロンテック
コーポレートセンター シニアITディレクター - 1974年4月、富士通に入社。開発製造部や製造技術部にて製品の設計・試作、FA(ファクトリー・オートメーション)やIE(インダストリアル・エンジニアリング)、ITを活用した工場の業務改革に従事する。1992年1月に生産部に異動し、システム担当部長として部品管理業務や生産業務の効率化をけん引。自動倉庫や電子看板の導入など、物流のJIT(ジャストインタイム)化を推進した後、2000年4月に生産技術部長に就任。翌2001年11月に富士通フロンテックへ転社し、情報システム統括部長兼SCM部長兼情報セキュリティ推進室長として、海外グループ会社を含む全社のIT戦略を統括する。2011年1月から現職。
─ サプライチェーンマネジメント(SCM)システム「iTOS(アイトス)」を稼働させて、予定よりも早く投資を回収することに成功したそうですね。システムの話をうかがう前に、まずはPOSやATMなどを製造する貴社の業界の近況を教えてください。
南里: (他の業界と同じく)国内だけでなく海外勢も強くなってきました。そうした中、収益力を高め続けるには抜本的にコストダウンを図る道を避けて通れません。何も変わらないまま業務を続けていれば、製品価格などの面でいずれ戦えなくなります。
─ 部品を共通化して資材調達コストを下げるなど、コストダウンにも色々な方法があります。
南里: 部品のコストダウンは収益力を上げる1つの方法ですが、打てる手はそれだけではありません。製造にかかわる非効率な業務を徹底的に排除し、間接費を下げることも重要です。
─ 直接原価だけを下げても収益力の維持・向上には限界がある。
南里: 間接費を下げなければ売上高が減った時に大きな打撃を受けます。逆に、間接費を押さえておけば売上高が減っても影響を最小限に食い止め、売上高が伸びた際には利益に貢献できる。
サイロ化したシステムが間接費を膨らませる
─ おっしゃることはよく分かります。ただ、間接費を下げると口で言うのは簡単ですが、製造業各社はかなり苦労されてきた。
南里: 私は間接費を下げるうえで、ITが強力な武器になると信じているんです。ただし、今までのように業務の部分最適を考えているようでは駄目です。サイロ化したシステムが増えるだけですから。もちろん、サイロ化したシステムにはノウハウが詰め込まれているので、個々のシステムを見れば素晴らしいかもしれませんが、問題も多い。
─ 例を挙げるとすると?
南里: 1つには、情報伝達のスピードが下がることがあります。これは非常に大きな問題です。
─ 情報伝達のスピード、ですか?
南里: 受注から出荷までの流れをイメージしてください。オーダーを受けて製品を作る場合、キャンセルや数量変更などで出荷時までにオーダー内容が変わることが多々あります。変動幅を小さくするにはオーダー確定の時期を出荷時期にできるだけ近づけたほうがよいのですが、情報伝達のスピードが遅いと変更内容を製造現場が吸収するまでに時間がかかるので、オーダー確定の時期を引きつけられない。
─ データ連携の仕組みを用意すればよさそうですが。
南里: それが部分最適で進化してきたシステムのもう1つの問題です。インタフェースの開発やテストに時間とコストがかかります。そもそも連携対象のシステムがすべてリアルタイムでデータ処理する設計ならともかく、バッチ処理で動くシステムが含まれていると情報伝達にどうしてもタイムラグが生じる。
─ もう少し詳しくうかがえますか。
南里: 生産管理と工場との間に1日のタイムラグがあったとしましょう。すると、生産管理は前日の情報に基づいて工場に生産指示を出さざるを得ません。仮に、工場に部品がないと倉庫に在庫を問い合わせ、在庫がなければサプライヤーさんに納期を確認する。こうした調整のやり取りはすべて人手で行うので、結果的に時間とコストがかかってしまうのです。
現場での経験が生んだリアルタイムへのこだわり
─ 南里さんは全体最適とリアルタイム処理に強いこだわりをお持ちのようだ。
南里: 昔からバッチ処理には違和感を覚えていた、というか単純にバッチ処理が嫌いなんです(笑)。
─ 何か苦い経験がありそうですね。
南里: ありました…。かつて生産管理の仕事をしていた頃の経験は、その1つです。サイロ化したシステムを使っている企業はどこも似たような悩みを抱えていると思いますが、オーダーや製造などの実績をバッチ処理で集計すると、必ずといっていいほど「オーダー数が合わない」「存在しないはずの製造番号が登録されている」などのエラーが出るんです。
─ 情報を入力する時点ではエラーが分からず、後になってドッとエラーが出てくる。
南里: それでエラーリストを1件ずつ見ながら、「情報が違っているようですが」と色々な部署に問い合わせて正しい情報を確認する。「どうしてバッチ処理の結果はいつも1回で合わないんだろう」と日頃から思っていました。
─ なるほど。
南里: 倉庫の業務を学ぼうと思い、上司に頼み込んで部品管理課に異動させてもらったときにも、リアルタイム処理の重要性を痛感しています。ご存じかも知れませんが、サプライヤーさんから届いた部品の受け入れ検査や生産ラインへの出材など、倉庫は製造にかかわる色々な組織と関連しています。それだけに倉庫には色々な問題が集積するんです。
─ いったい倉庫で何が起きていたのですか。
南里: ひと言で言うと、モノと情報の不一致です。納期に間に合わせるため、製造現場では倉庫に部品が届くと急いで受け入れ検査を済ませ、1個でも2個でも早く生産ラインに送らなければならないことがあります。本来は伝票処理をしてから運ばなければならないところ、時間が許さないので伝票処理が後回しになる。これではモノと情報の流れが一致するはずがありませんよね。
─ モノはリアルタイムで動くけど、情報は遅れて流れるわけですから。
南里: 先ほども触れましたが、モノと情報が合っていない状態のまま生産管理から部品の出材指示が出ると、倉庫では「部品が5個足らない」ということになります。そうなったら部品管理課は大変です。「きちんと受け入れ検査したのか」「どこかに置き忘れていないか」と怒られましてね。
─ 管理のやり方そのものに問題がある気が…。
南里: あ、いずれも昔の話ですよ。でも、そうした経験を通じて、モノと情報の不一致を完全に解消するには、モノの動きに合わせて逐次情報を取る以外に方法はないと確信するようになりました。しかも、倉庫などの業務に閉じた環境ではなく、生産管理や工場、サプライヤーさんまで一貫して共通の情報に基づいて活動する必要があると。
─ その思いを実現するために開発したのが、今回のiTOSというわけですね。
南里: おっしゃる通りです。
●Next:生産ラインとサプライヤーを「RFIDかんばん」で結ぶ
会員登録(無料)が必要です
- 1
- 2
- 次へ >
- 「こんな旅がしたい!」をチャットの対話で提案、Booking.comが挑むAI駆動の旅行計画(2025/08/05)
- 脆弱性対処を10日から3日に─JERAが実践するマルチクラウド環境のセキュリティ強化(2025/07/31)
- コラボレーション・自動化・AI─全社ファイル管理基盤を核にしたオンワードグループのDX実践(2025/06/30)
- 『モンスターハンターワイルズ』の開発で、カプコンのITチームが重視したこと(2025/06/11)
- 生成AIとロボットの融合で新たな価値創造に挑む─デンソーが描く近未来(2025/04/22)