製品をマーケットに、いかに早く届けるか−−。こうした観点から、製造拠点を海外に設ける製造業は珍しくはない。日立製作所の情報・通信システム社も、その1社。サーバーやストレージ製品の製造拠点を、日本、米国、仏の3カ所に置いている。現在は、3拠点体制のメリットを活かすために、製造実行システム「MES(Manufacturing Execution System)」の共通化を図り、3拠点同時の量産立ち上げを実現している。仏ダッソー・システムズのイベント「3D EXPERIENCE FORUM Japan 2015」に登壇した日立ITプラットフォーム事業本部グローバルサプライチェーン本部の松尾 邦之 本部長の講演から、同社の取り組みを紹介する。
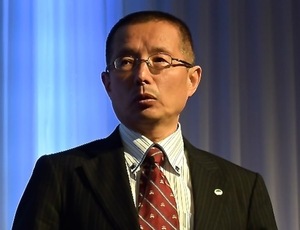
日立製作所の情報・通信システム社は、IT関連の製品・サービス事業を担う社内カンパニー。日立の全売上高の19%を占め、セグメント別では最大規模である。松尾 邦之 本部長が属するITプラットフォーム事業本部は、サーバー(Unified Compute Platform、BladeSymphony、HA800など)、ストレージ(Unified Storage、Virtual Storage Platformなど)、ソフトウェア(JP1、Cosminexusなど)などを開発・販売している。
これら製品群のうち、サーバーとストレージのハードウェアにおいては、開発は日本で実施したのち、日本と米国、フランスの世界3カ所に生産拠点で製造している。現在は、製造実行システム「MES(Manufacturing Execution System)」の共通化を図ることで、設計後には世界同時に量産体制を立ち上げられるようになっている。
MESは、主に製造業の工場で使用されるシステムで、製造工程の各部分とリンクすることで製造状況を把握したり管理したりするための仕組みだ。作業手順から入出荷、品質管理、保守、スケジューリング、トレーサビリティといった機能を持ち、ERP(Enterprise Resource Planning)と連携させて利用する。そのため、製造現場と経営管理をつなぐソリューションと呼ばれる。
日本では、経験を持つ現場技術者による納期や品質の管理が一般化していたため一気に普及することはなかった。それが、西暦2007年問題により経験のあるベテラン技術者が大量に退職し始めたたことで、管理のシステム化が急務になり、MESの導入が進んだとされる。海外生産拠点が増え“あうんの呼吸”による管理が難しくなったこともMES普及の一因になっている。日立の場合も、このケースに当たる。

拡大画像表示
利用しているMESは仏ダッソー・システムズ製の「DELMIA Apriso」。MESの標準化団体である「MESA」が定める11の標準機能に加え、在庫管理やラベル印字といった拡張機能を使っている(図1)。
MESAが定める11の機能とは、プロセス管理、トレーサビリティ、リソースアロケーション、データ収集、品質管理、設備保守・保全管理、OP&スケジューリング、オーダーコックピット、ドキュメント管理、従業員管理、性能モニタリングである。
サーバーのグローバル生産体制は6カ月で立ち上げ
グローバルでのMES共通化によって、日立が得ているメリットは大きく4つある。1つが、新製品の3拠点同時量産出荷の実現だ。生産開始前から生産プロセスを拠点間で議論し、3拠点同時に生産を開始することで、「GA(General Availability=正式版)リリースから1カ月後には、全3拠点で新製品を同時出荷している」(日立ITプラットフォーム事業本部グローバルサプライチェーン本部の松尾 邦之 本部長)。
従来は、評価版リリース後1カ月で日本で量産が始まり、2カ月後に国内およびアジア向けに出荷。その後に欧米拠点での量産を開始していたため、全3拠点で量産が始まるまでに4カ月を要していた。
2つ目は、上記体制をサーバー製造に短期間に適用できたことだ。3拠点での生産はストレージから始まり、サーバーは日本の秦野工場でのみで生産していた。しかし、サーバーにおいてもTTM(Time to Market)、TTV(Time to Volume)を実現するために、2014年からサーバーも3拠点生産とし、わずか6カ月でMESを使った3拠点での同時量産体制を構築している。
3つ目は、製品の「親子体系での在庫管理により、組み立てから出荷までの作業時間を50%低減した」(松尾本部長)こと。ラック型サーバーのラックフレームを「親」、コントローラーやハードディスクなどの部品を「子」として在庫管理することで、CTO(受注生産:Configure to Order)時のシステム構成をシミュレーションし、作業の短縮を図る。
具体的には、試験用である「仕込み生産」したものを、解体し各部品単位に保管することを止め、そのままの製品構成で保管。CTOでは、顧客が希望するシステム構成をシミュレーションし、それに最も近い親子構成の在庫を選び出して、完成させる。
最後は、「MESにおけるモジュラーコンセプトの開発フレームワークの活用」(松尾本部長)だ。MESの3拠点への導入では、システムを分業体制で開発した。その際、ダッソーの画面開発・制御フレームワークである「Screen Framework」を使うことで、他拠点で開発した仕組みに対する修正を容易にした。開発生産性をより高めるため、画面・サブルーチン間の呼び出しをマスター制御するためのツール「Application Configuration」を内作している。
多拠点化で調達効率は高まったが製造プロセスは現地任せに
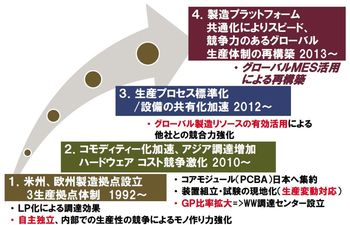
拡大画像表示
同事業本部が、日米欧の3拠点体制を敷いたのは1992年のこと(図2)。ストレージ製品が対象で、日本・中国・アジアパシフィック向けを神奈川県小田原市の工場で、北米・南米向けを米国のオクラホマ工場で、欧州・アフリカ向けは仏のオルレアン工場で生産する。サーバーは、神奈川県秦野市のみで生産する1拠点体制だった。
3拠点化により、資材の現地調達(LP:Local Procurement)が進み、調達は大幅に効率化が図れた。一方で、各拠点の自主独立性が強く、拠点間で生産性の高さを競い合い、それぞれが改善活動をどんどん進めていったことで、「個々には良い面がある反面、統一性がなくなるという弱みもあった」(松尾本部長)。
2010年頃になると、ハードウェアのコモディティ化が加速しコスト競争が激化、部品の調達先がアジアに集中してきた。そのため、投資額が大きいコアモジュールの生産は日本に集約。装置の組み立てとテストなどは、顧客が求める納品スケジュールが短期化していることを受けて、従来通り各拠点で実施するようにした。
さらに2012年からは、競争力強化のため、同じ製品の生産でも微妙に異なっていた生産プロセスや生産設備の標準化を進めることにした。しかし、地域によって生産量に差があり、売れ筋の製品も異なるため、どうしても「個性を出したい」という希望が各拠点から上がってくる。
MESも、各拠点が個別に異なる仕組みを導入しており、機能や拡張性、グローバル対応の欠如、情報の分散といった課題を抱えていた。具体的には、日本では某メーカー製と自社開発のMESを、オクラホマではApriso製品を(のちに仏ダッソー・システムズが買収)、オルレアンでは自社開発のMESをそれぞれ使っていた。
会員登録(無料)が必要です
- 1
- 2
- 次へ >
- 「こんな旅がしたい!」をチャットの対話で提案、Booking.comが挑むAI駆動の旅行計画(2025/08/05)
- 脆弱性対処を10日から3日に─JERAが実践するマルチクラウド環境のセキュリティ強化(2025/07/31)
- コラボレーション・自動化・AI─全社ファイル管理基盤を核にしたオンワードグループのDX実践(2025/06/30)
- 『モンスターハンターワイルズ』の開発で、カプコンのITチームが重視したこと(2025/06/11)
- 生成AIとロボットの融合で新たな価値創造に挑む─デンソーが描く近未来(2025/04/22)